- Katolight Automatic Engine Control Manual Free
- Katolight Automatic Engine Control Manual Transmission
- Katolight Automatic Engine Control Manual Pdf
- Katolight KDGC-500 may also be labeled as Basler DGC-500 or Coleman KDG-500 KDGC-500: The most common failure is lightning damage on Prog Inputs (P2-P3-P4) and Oil Sensor input (P-13). As part of our one year guaranteed repair service, we add electrical spike and surge protection to these terminals.
- KATOLIGHT D125F.J4 Diesel Gen-Set STANDARD EQUIPMENT CONTROL PANEL - Model #45 control panel - AC voltmeter, 3 1/ 2, 2% accuracy - AC ammeter, 3 1/ 2, 2% accuracy - Combination VM/AM selector switch, 4 position - Frequency meter, 3 1/ 2, 55-65 Hz. Vibration shock mounts (4) - Engine control - KASSEC-12 or 24 VDC, with cyclic cranking timer.
Katolight model 130 automatic engine control board base fuel tank, john deere engine katolight generator manuals 105 kw katolight diesel Steadypower.com - Search Results for ' katolight Search Results for 'katolight 25kw pto generator' Transfer Switches Manual Generator Ready Load. // KASSEC automatic start engine control (12 or 24 volt DC) // Battery charging DC voltmeter: 2' // Engine coolant temperature gauge: 2' // Engine oil pressure gauge: 2' // Running time meter: 2', 5 digits // Alarm buzzer with silencing switch // 3 position mode switch (auto-off-manual) // Approximately 30 lbs. // Complete package.
The main function of a generator auto start is to automatically start & stop a generator. This is accomplished by following our generator auto start circuit diagram. Then, you are required to set up parameters and configure inputs connected to level switches, pressure switches, climate control systems, mains failure detection relays or other. A generator auto start can automatically start the engine when battery is low or when you trigger the remote start input. It will automatically stop the engine after a programmable time or when the battery are full charged. You can observe the connections of the KEY-SWITCH [10] in case you prefer a manual key start. You are required to use pilot relays to drive solenoids to start and stop the engine [7]. In the following diagram, the outputs of the controller are positive. You are required to connect to battery minus the other side of each relay coil. The use of flywell diodes is highly recommended. The inputs [18] (analog and digital) provides protections against dangeros situations (oil pressure for example or if temperature exceeds the limit). A generator auto start features a serial interface that allows you to remotely control and monitor the generator. In the following generator auto start circuit diagram you can observe the serial interface RS485 [8] and the connections of the CANBUS [9].
The Be24 generator auto start circuit diagram is a simple and intuitive diagram. The generator (1) voltage is connected to L1 & L3 via protection fuses (4). The Generator Circuit Breaker is driven by the digital output '2'. The dashboard is supplied by the terminal blade 15/54 via a 5 Amp fuse. You can monitor the generator current by using a current transformer of suitable size connected to S1 and S2. The outputs of the controller [6] need a pilot relay. The use of fly back diodes is mandatory. The Be24 detects the rotational speed from a pick-up or from the 'W' terminal of the belt alternator [10] [12]. If these devices are not available, the Be24 automatically calculate the rotational speed from the generator. The inputs [8] (digital) provides protections against dangeros situations (oil pressure for example or if temperature exceeds the limit) and allows you a remote start by using a simple switch (REM). You can configure the REM INPUT norlally closed or open.
GENERATOR AUTO START CIRCUIT DIAGRAM: INPUT FUNCTIONS
What about the Auto Start inputs ? The minimum configuration should be the following
- two configurable digital inputs to start the engine
- two configurable inputs for stop and emergency
- three digital inputs to protect the engine (oil pressure switch.other.)
- three analogue inputs to protect the engine (temperature, fuel level..)
- one input to monitor the charger alternator (to detect the engine running status)
- one digital input (optional) to monitor a magnetic Pick-up.
Katolight Automatic Engine Control Manual Free
- one analogue input to monitor the Belt Charge Alternator
GENERATOR AUTO START CIRCUIT DIAGRAM: OUTPUT FUNCTIONS
What about the Auto Start outputs? The minimum configuration should be the following:
- one digital output for fuel solenoid (energized to run)
- one digital output for STOP solenoid (energized to stop)
- one digital output to drive an audible alarm signal
- two digital outputs for Preglow-Prelube (Diesel Engine)
- two optional outputs to repeat some alarms of flags
- one digital output for START solenoid (energized to start)
- one 3-Watts Power Dc output to excite the Belt Alternator
- one digital output to control the CHOKE (gasoline engine)
- one digital output to control the GAS valve (gas engine)
It is preferable a Generator Auto Start Module with static & short circuit proof outputs. External relays could be placed in proximity of the engine or generator. Automotive Plug-In relays are always preferable. In case of damage you can replace the relay (it is really easy to find automotive relays in a shop for auto parts & accessories). A Bernini Design Generator Auto Start Module works in a range of about -20 up to plus 70 degree Celsius. The electronic circuitry is designed to work in between 5Vdc up to 33Vdc and able to survive in case of total battery loos for about one second. A Bernini Design Generator Auto Start Module provides high resistance to fatigue due to the key start.
The Generator Auto Start releases the user from boring manual activities. A mandatory feature of an Generator Auto Start, anyway, is to provide a full manual control of the system. This could be useful in emergency situations or when you need to take priority over the automatic system of operation. A Bernini Design Generator Auto Start includes many programmable parameters. There you are here the most used:
START DELAY TIME >It provides a programmable delay after detecting a start condition request on a programmable input (or serial interface).
STOP DELAY TIME >It provides a programmable delay after detecting a stop condition request on a programmable input (or serial interface).
PRE-LUBE TIME >It energizes the Pre-lube pump or simply it could be used to delay the crank if necessary.
PRE-GLOW TIME >It energizes the Pre-glow of the diesel engine.
PRE-GLOW MODE >It allows you to choose the best pre-glow logic .
CHOKE TIME Manager for mac 10.6 8. >It energizes the Choke of gasoline engine for a programmed time.
CRANK VDC >It terminates the crank when voltage of the charger alternator rises above the setting. The option OFF disables the monitoring.
CRANK VAC >It terminates the crank when voltage of the generator rises above the setting. The option OFF disables the monitoring.
CRANK TIME >It limits the coupling of the starter motor.
CRANK REST TIME >It creates a delay after each starting pulse in a way to stabilize the parameters of the battery. In the same time it cools down the starting motor.
START ATTEMPTS >It limits the numbers of attempts before providing a starting failure alarm.
CRANK HZ > It terminates the crank when frequency of the generator rises above the setting. The option OFF disables the monitoring.
CRANK RPM > It terminates the crank when the rotational speed of the engine rises above the setting. The option OFF disables the monitoring.
Katolight Automatic Engine Control Manual Transmission
Cara corel draw gratis. The above parameters are normally 'factory defined', but a Bernini Design Generator Auto Start module will let you full access to the settings. You can adapt the AGS to any style of engine and generator.
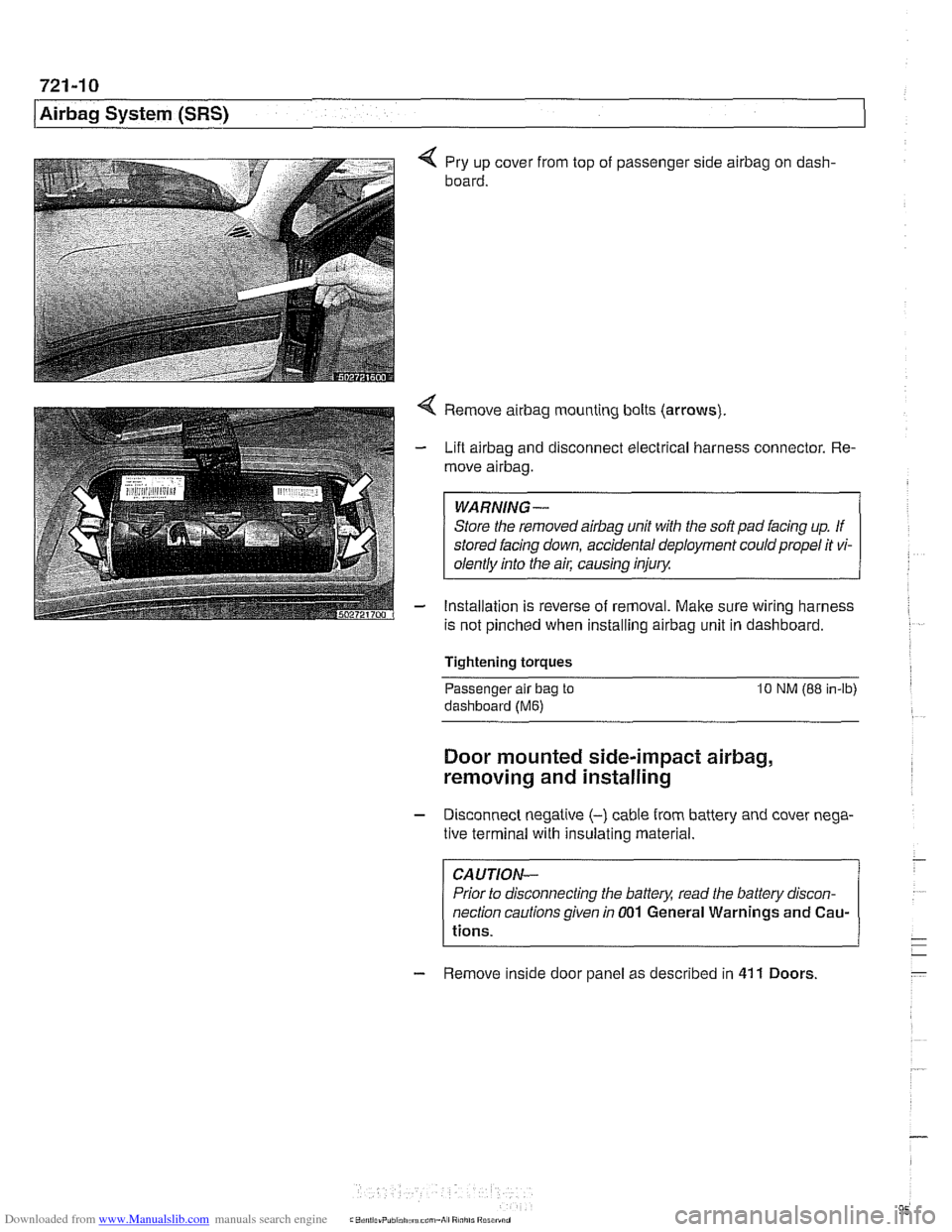
Follow these links to see the list of all adjustable parameters!
Understanding a generator remote start circuit. In this explanation we use the Be1 Auto Start Module. The principle is the same using Be124 and Be24. When the engine is not running, the voltage of the terminal D+/WL (yellow wire) of the charger alternator is closer to zero volt (0V). As soon as the Be1 starts the engine, a voltage appears in the D+/WL terminal (0,8 to 2,5V). This is due to the exciting current that flows into D+/WL from the Be1 alternator excitement circuit. When the engine starts running, the voltage of the D+/WL terminal increases by up to 3V-6V. This usually happens around 500 up to 800 RPM. When the engine runs at nominal speed (1500 RPM for example), the D+/WL voltage reaches the 14V (or 28V in case of 24V system) needed to charge the battery. The safest point to disconnect the starter motor is between 6V to 10V (500-800 R.P.M). The default parameter of [P24], or factory setting if you will, is 8.0V. Make sure that the green ‘START-ON' LED on the front panel is off during the all starting attempts.The Be1 can display the charger alternator voltage (see section 3.0 of the User Manual). The value of it can help you in troubleshooting a problem of the charger alternator. The Be1 also uses the speed measurement (RPM), Alternator voltage (V generator) and Generator frequency (Hz) to terminate the crank. The user manual explains all details.
USING A FLYWHEEL GENERATORThis is the case of gasoline engines or some the case of small size diesel engines. The Be1 controller features DC and AC inputs to monitor the charger alternator. A gasoline engine is not fitted with a belt driven charger alternator (does not exist the D+/W.L. terminal) because it uses a flywheel generator that provides an AC voltage. We recommend that you disable the [P25] ( [P25]=OFF). This prevent the Be1 to monitor the 'BROKEN BELT' alarm. Connect the floating charger wires directly to terminals 15 & 16 of the Be1. You cannot monitor a FLYWHEEL GENERATOR using BE24 or BE124 except the case when the engine is fitted with a charger regulator that provides the W.L. simulator terminal (normally suitable to drive a lamp). In case of a flywheel charger generator (this is normally the case with gasoline engines), the reading of the charger voltage is not accurate. The [P24] setting, in this case, expresses only a proportional factor. As a matter of fact the voltage is alternate, it is not stable, and the frequency depends on the kind of engine. Be1 is able to detect the proper moment to disconnect the crank. You are requested to change the setting from 8V , down to 5V or 6V if necessary. You have to find the correct setting. The Be1 user manual will guide you via a step-by-step procedure.
ABOUT GENERATOR AUTO START MODULESBernini Design offers the best generator auto start circuit diagram suitable for your application. If your business is about small up to medium size gasoline generators we recommend that you use the Be1 generator auto start module. The generator auto start circuit diagram about it is really simple and intuitive. You can connect the Be1 module to an external controller, for example an Automatic Mains Failure module or Automatic Transfer Switch. If you business is about industrial application of heavy duty application you may use the Be24. It is suitable for a diesel engine. It features a strong key start module. This controller is extremely user-friendly. You can feel like using your car. But if you are looking for the best generator auto start module you have to use the Be124 controller. It provides all kind of functions including oscilloscope and data logger.
Katolight Automatic Engine Control Manual Pdf
The instruction manuals and drawings listed below are in PDF format. All documentation is in English unless otherwise indicated. Instruction manuals and drawings not listed here are subject to availability.
Contact us to request documentation for a specific generator. In your request, provide both the serial and model numbers located at the top of the nameplate. Documentation for serial numbers prior to 70000 is subject to availability.
Documentation for complex units, including motor-generator sets with controls, is subject to availability and may incur a reproduction fee. Printed copies of instruction manuals and drawings are subject to printing and shipping fees. A quote is provided for work incurring fees prior to any work performed. We accept American Express, Visa, and MasterCard.
Please contact us with any questions or to request documentation.
Kato Engineering Inc.
P.O. Box 8447
Mankato, MN 56002-8447
USA
Tel: 507-625-4011
Fax: 507-345-2798
Email:KatoManuals@mail.nidec.com
Generators | ||
350-01001-00 | 634 kB | Standard ac generator, single or two-bearing, drive-end air discharge |
350-01001-00 FR | 793 kB | Standard ac generator, single or two-bearing, drive-end air discharge (in French) |
350-01001-00 RU | 1,560 kB | Standard ac generator, single or two-bearing, drive-end air discharge (in Russian) |
350-01001-00 SP | 1,450 kB | Standard ac generator, single or two-bearing, drive-end air discharge (in Spanish) |
62047802 | 1,603 kB | Packaged generator (has 'MTG' in nameplate code) |
350-01015-00 | 534 kB | AC generator with center air discharge |
350-01016-00 | 541 kB | AC turbine generator |
350-03001-00 | 1,648 kB | MG set, brushless generator, induction motor |
350-03006-00 | 812 kB | MG Set (brushless, synchronous) |
352-50300-10A | 2,474 kB | Brushless AC rectified DC traction alternator |
INS-51C-65 | 2,016 kB | AC generator with direct-connected brush-type DC exciters |
KAMAG generators and electrical connection drawings | ||
350-04001-00 | 2,242 kB | KAMAG single bearing with outboard exciter |
350-04002-00 | 1,784 kB | KAMAG two bearing with outboard exciter |
P8800-479 | 137 kB | Electrical connection drawings for KAMAG 14 @ 18 w/KAMAG I Regulator |
P8800-618 | 181 kB | Electrical connection drawings for KAMAG 14 @ 18 w/KAMAG I Regulator, newer |
P8800-641 | 189 kB | Electrical connection drawings for KAMAG 14 @ 18 w/KAMAG II Regulator |
P8800-728 | 171 kB | Electrical connection drawings for KAMAG 14 @ 18 w/KCR Regulator |
P8800-826 | 151 kB | Electrical connection drawings for KAMAG 14 @ 18 w/VR63 Regulator |
P8800-837 | 132 kB | Electrical connection drawings for KAMAG 22 w/APR63 Regulator |
P8800-838 | 144 kB | Electrical connection drawings for KAMAG 14 @ 18 w/APR63 Regulator |
P8800-840 | 139 kB | Electrical connection drawings for KAMAG 22 w/KCR-360 Regulator |
P8800-841 | 108 kB | Electrical connection drawings for KAMAG 14 @ 18 w/KCR Regulator, dual rated CB |
Voltage regulators | ||
351-01057-00 | 1,568 kB | K65-128B & K125-10B voltage regulators |
351-01015-00A | 1,617 kB | KCR 160 voltage regulator |
351-01001-00B | 901 kB | KCR 360 voltage regulator |
INSR-23-71A | 1,899 kB | KCR 560 voltage regulator |
351-01002-00A | 1,510 kB | KCR 760 voltage regulator |
351-01021-00 | 2,056 kB | KAMAG voltage regulator |
INSR-9-78D | 1,414 kB | KAMAG II voltage regulator |
351-01055-00 | 183 kB | Dual automatic voltage regulator |
351-01004-00 | 724 kB | Voltage regulators (P/N 800-84132-07 and 80084132-11) |
351-01052-00 | 1,133 kB | Mag Amp voltage regulator, single phase (800-84132-XX) |
351-01053-00 | 177 kB | Mag Amp voltage regulator, three phase (800-84132-XX) |
351-01006-00A | 1,658 kB | Voltage regulator (800-84132-10 and 800-84132-13) |
Miscellaneous controls | ||
351-02003-00 | 417 kB | Auto manual module (several part numbers) |
351-02014-00 | 491 kB | Diode fault detector |
351-05003-00 | 36 kB | Over-under voltage relay |
351-05010-00B | 410 kB | Field failure and out-of-step protection assembly for synch motor (P/N 511-01111-25) |
351-05024-00 | 1,119 kB | Field failure and out-of-step protection assembly for synch motor (P/N 511-01111-26) |
351-05027-00 | 803 kB | Voltage frequency sensor (511-01840-XX) |
351-05028-00 | 978 kB | Excitation sensor and reverse power relay (511-00820-01 and 511-00280-02) |
351-07002-00 | 1,229 kB | Line drop compensator (514-01905-04, 514-01906-04, 513-01907-04) |
351-09002-00 | 750 kB | Cross-current analyzer |
508-00470-60/61 | 151 kB | Paralleling module |